Disks of Unequal Sizes
It sometimes happens that the tool and mirror blanks may not be of exactly equal diameters. A difference of about 1/8″ does not matter, as the working surface of either disk can be beveled by whatever amount is needed to make them both equal.
Broken Disks
Occasionally, before completion of the mirror, either it or the tool may be broken. If this happens to the tool in the polishing stage, a flat iron disk or another glass disk can be obtained, and a new lap made on one of its flat surfaces. The greater thickness of pitch at the center will introduce no difficulties, and polishing and figuring can be successfully concluded.
If the tool is broken before grinding is completed, the mirror must be ground with No. 80 on top of the new tool, using one-half diameter strokes, until the grinding reaches the center of the tool, when the radius of the mirror should be measured, and the procedures outlined in Chapter 4 then applied.
If it is the mirror that is broken, rough grinding of a new blank on the already curved tool may begin with half-diameter strokes, in which the center of the mirror traverses a zigzag course like that shown in Fig. 30. If the resultant curve becomes too shallow, increase the amount of work over the edges of the tool; if too deep, work more over its center. When the curve has been extended to about 1/16″ from the edge of the mirror, resort to one-third strokes to bring the surfaces spherical.
Concrete Suggestions
The concrete for the base of the grinding stand (Fig. 17) should be a rather stiff mix, of parts 1, 2, and 4, of cement, sand, and gravel. Keep it moist for several days while curing. The base for the concrete pier for a permanent mount can be of a leaner mix, 1, 2, and 6. Brick and stone can be used as a filler. The pier, of course, should be of the stronger 1, 2, and 4 mix.
The bolts holding the mounting to the pier can be quite accurately bedded in the concrete in this way: Transfer the holes from the heavy flange (A, Fig. 72) to each of two plates of sheet metal, one of which has been cut away to a skeleton shape. First pass the four bolts through the corner holes of this skeleton plate and screw nuts onto the threaded ends. Fit the other plate down against the nuts, apply four more nuts, and lock the second plate tight. Then set the assembly, skeleton plate down, in the wooden form and orient it carefully as explained in Chapter 17. After the concrete has hardened, the upper plate and the nuts can be removed, and the mounting can be set down.
Blind Flanges
As a rule, the holes found in heavy flanges are much larger than are needed, so a blank or “blind” flange should be asked for. If the dealer does not have it in stock, let him order it. Holes of the correct size can then be drilled, but they must be slightly larger than the bolts (which might be ⅝” in diameter), to permit tilting for latitude correction.
Springs
For the mirror cell and other parts, if compression springs of just the right length cannot be found, longer ones can be cut off by holding a coil against the corner of a grinding wheel.
Working Time
The question is often asked, “How long does it take to make a mirror?” This is largely a matter of experience. A woman student finished her first mirror in the exceptionally fine time of about 25 hours. Confronted with the necessity of replacing a broken mirror, the author completed a 6-inch f/8 in two evenings. a total of about eight hours’ working time. On the other hand, mirrors have been known to take two years or more. Figuring can well consume the bulk of the time put in. The curve should be achieved in two or three hours, and allowing a liberal hour for each of the stages of fine grinding makes a total of eight hours for grinding. Lap making, one hour, and six hours for polishing, brings the total time up to 15 hours. Figuring, x hours. The average amateur, working alone, from the directions given in this book, should complete a good mirror in from 30 to 40 hours of working time. Making the diagonal is a much simpler proposition. Here one is concerned only with the small piece of glass at the center of a large disk. Thirteen diagonals, cemented to an 8″ disk, and ground and polished in conjunction with two other disks in the manner described for making optical flats (Appendix B), were completed by the author in a total of about 10 hours, the surfaces of the diagonals being flat to a quarter wave or better.
Observing the Sun
Never attempt to view the sun directly through the telescope without first doing something about the terrific concentration of heat and light, else the penalty may be a hole burned in the retina, perhaps permanent blindness. This warning can be modified to the extent that the setting sun, when it appears dull and coppery, hanging just above the horizon, may be looked at with the aid of a piece of smoked glass or other filter held between the eyepiece and the eye. When it is higher in the sky, the sun may be observed only when complete protection has been afforded the eye.
An Exclusively Solar Telescope
But if the telescope is to be used only for solar observations, the full resolving power of the mirror can be retained by coating the primary and secondary mirrors, not with a reflecting substance, but with the anti-reflecting magnesium fluoride. The net result is that only a fraction of one per cent of the light striking the main mirror reaches the eyepiece, but a few niters may still be required. The back surface of the diagonal should be rough ground and painted black to cancel out any reflection from that source. Better still, instead of the ordinary diagonal, is the Herschel wedge. As its name implies, this is a wedge-shaped glass prism devised by Sir John Herschel; its back surface is so inclined that any reflection from that source is pitched out at a radically different angle to that from the first surface, and so it does not interfere with the vision. If a right-angle prism is used for the secondary reflection, its hypotenuse or reflecting surface should face outward, so as to reflect externally.
A Too-bright Moon
Lunar observation, ordinarily rather trying on the eyes, and at times very much so, can be rendered more comfortable by the introduction of some of the filters or stops described above.
Suns Pot Projection
Sunspot observation can be enjoyed by several persons at the same time simply by projecting the sun’s image onto a white cardboard screen. The eyepiece (a low power is best) is used as a projecting lens by drawing it slightly out of focus. By changing the eyepiece position and adjusting the distance of the screen to suit, the size of the projected image can be varied. This method is awkward unless a support for the screen is made. A more satisfactory device is a box, light-tight and light in weight, that can be strapped to the telescope straddling the eyepiece, the bottom or outer surface of the box being formed of a sheet of ground glass onto which the sun’s image is projected. Means of access should be provided for adjusting the eyepiece.
Plastic Lenses
With the advent of transparent, easily worked plastic materials, it was inevitable that the use of plastics as a substitute for glass would be sought by the optical industry. The wartime requirement for mass production of optical elements resulted in considerable advance in techniques for making lenses and prisms of plastic.
Among the properties of plastics requiring investigation were dimensional stability, surface hardness, tensile and impact strength, shrinkage, coefficient of expansion, water absorption, heat distortion, resistance to chemicals, internal homogeneity, transparency, and scratch resistance. In all of these characteristics, glass rates favorably, and it is not surprising that a perfect plastic substitute has not been found.
Among the most suitable plastics for optical purposes are methyl methacrylate (lucite), cyclohexyl methacrylate (CHM), and styrene. The last two have been widely used together to make achromatic lenses for military optical instruments of low power. The elements have been produced by casting in molds of pyrex or steel, the cast surfaces of the plastic requiring no further finishing.
Processes have been developed for increasing the surface hardness of the finished plastic elements by 15 to 30 times. Nevertheless, because of their low resistance to abrasion, it is still necessary either to confine plastic lenses to the interior elements of optical systems or to protect them with plane-parallel cover glasses.
The most recent and possibly the best method of producing plastic optical elements of precision is to grind and polish them to curve, in much the same manner as glass elements are manufactured. For this work special abrasives have been developed. Lenses as large as 18″ in diameter have been made, and larger are on the way. Mirrors and correcting plates for Schmidt cameras have also been made (by the molding process as well). Because they cannot be economically produced in diameters of less than 2½”, plastic lenses made by the new method are not likely commercially to replace glass lenses in binoculars or small cameras, although excellent results have been obtained with camera objectives composed entirely of plastic elements.
The accuracy obtained by current methods is .said to be within a few wave lengths of light, and the plastic elements are fully stable at temperatures up to 150° F. The long-chain molecular structure of all plastic materials, however, makes it improbable that plastic lenses can ever be used for astronomical telescopes or other instruments where extremely accurate image formation is demanded.
Fluoride Coatings
When a hard permanent fluoride coating is applied to optical surfaces, the temperature of the glass must first be brought up to about 400° Fahrenheit. This cannot be very quickly done, and is quite a slow process in the case of thick mirror disks. Some technicians may be unwilling to wait the required time, in which event the fluoride coating will be too soft, affording no protection to the aluminized surface, and coming off with the least bit of rubbing. Unless assurance can be had in advance that a durable coating will be furnished, the money spent may be wasted. If the job is properly done, the coating should be able to withstand vigorous rubbing with soft cotton or tissue. There should be no excuse for failure with the secondary mirror, however, which is as easy to treat as the average lens or prism, and as the secondary is at the dewy and dusty end of the telescope, it should be good economy to fluoride-coat its aluminized surface.
Tying the Tripod Legs
To prevent the tripod from collapsing, the legs must be securely linked together. One method is to run separate lengths of chain or flexible cable from leg to leg, or to each leg from a common center. An alternate method is to use rigid members of wood or metal, either joining leg to leg or running to a common central junction. The flexible ties are easiest to install, but rigid ones will lend added stiffness to the tripod.
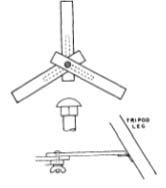
An excellent method of securing the legs is shown in Fig. 98. The hardwood ties, of suitable length, and about ⅜” thick by about 11/4″ wide, are joined to the legs by ordinary hinges. A ⅜” carriage bolt (see inset) and wing nut lock the three ties in a common union at the center. The spread of the legs can be varied if slots, indicated by the dotted lines, are sawed or milled in the ties. Since the latter are each in different planes of elevation, they must be hinged to the legs at appropriately spaced intervals, and the leg attachments must be designed with this end in view.